What it’s all about
Predictive maintenance allows predictions to be made about the service life and maintenance of equipment based on its condition, using machine data.
Sensors or the programmable logic controller (PLC) in the equipment provide vast amounts of data. The data is collected, processed, and archived. The archived data can be analyzed to show the equipment’s condition and how “healthy” it is.
How we can help you
We deliver turnkey software and hardware solutions to your exact specifications from a single source – from the simple to the highly complex.
With our expertise, we can give you professional advice on planning your digitization work in the manufacturing or maintenance environment.
Our solutions can be integrated into brownfield projects and are also suitable for getting started in greenfield facilities. Discover the scalability of our SOMA software platform for yourself.
SOMA – the software platform for predictive maintenance
The SOMA platform
SOMA can be custom-integrated into your production landscape (MES/ERP) and, thanks to amazing scalability, can be adapted to your growing requirements – starting with monitoring by an operating hour meter through to high-resolution sensor data.
Everything is modular, so you only purchase and pay for what you currently need for your production or maintenance.
That means functions can be upgraded easily and cost-effectively. Your digitization can grow with you.
Your benefits: Predictive maintenance with SOMA
The technology behind your route to more efficient production:
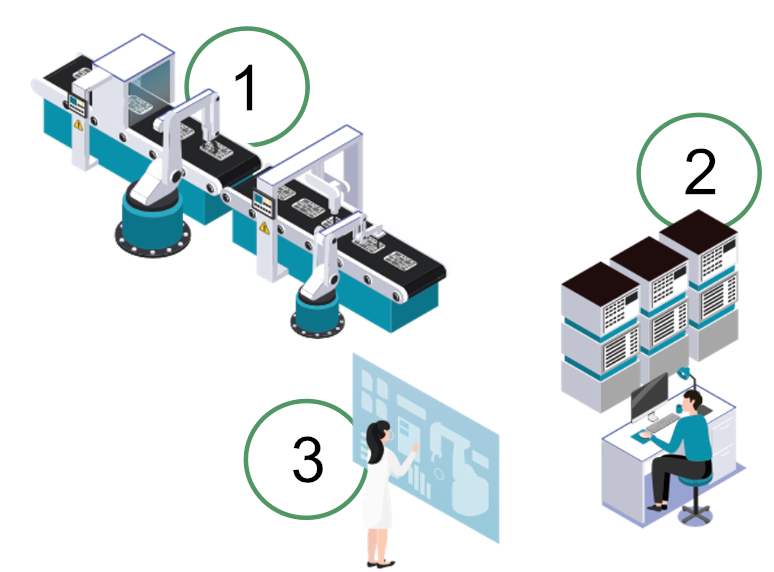
The data is collected from SOMA edge devices (industrial PCs) via, for example, a bus system, from your machine PLC, or by external sensors, which we can retrofit for you. Data preprocessing and characteristic value computation is carried out on the SOMA edge devices, minimizing data transfers for long-term data archiving on the server.
The SOMA edge devices send the collected data to a central server of your choice (cloud or on-premise) for long-term archiving. The data is accessed via the SOMA web server using a standard browser, such as Google Chrome.
The analysis and evaluation models, e.g., for predictive maintenance, process data, or energy monitoring, are customized and made available from the SOMA web server. The associated visualization is individually configured on the basis of your equipment and data to ensure maximum ease of use.
Based on the collected data and underlying prediction models, the software creates a clear presentation of maintenance requirements in the form of a traffic light system as a function of configurable threshold values. Model expertise is therefore not required and misinterpretations are minimized.
Maintenance recommendations or alarms are automatically sent to the relevant maintenance personnel via SMS or email. In addition, all current and historical data as well as the remaining service life of the components can be monitored in a configurable dashboard on each end device via a browser. That means a dynamic maintenance plan can be generated at the push of a button.
References and use cases
Contact us:
Please feel free to reach out to my team and me with your project requirements. We would be happy to give you an initial overview of how our experienced developers can meet your individual goals.